當前位置: |
引領中國冶金邁向智能化、綠色化、低碳化、高效化------ 中冶華天一批煉鐵核心技術達國內(nèi)國際先進水平
發(fā)布日期:2022-07-20
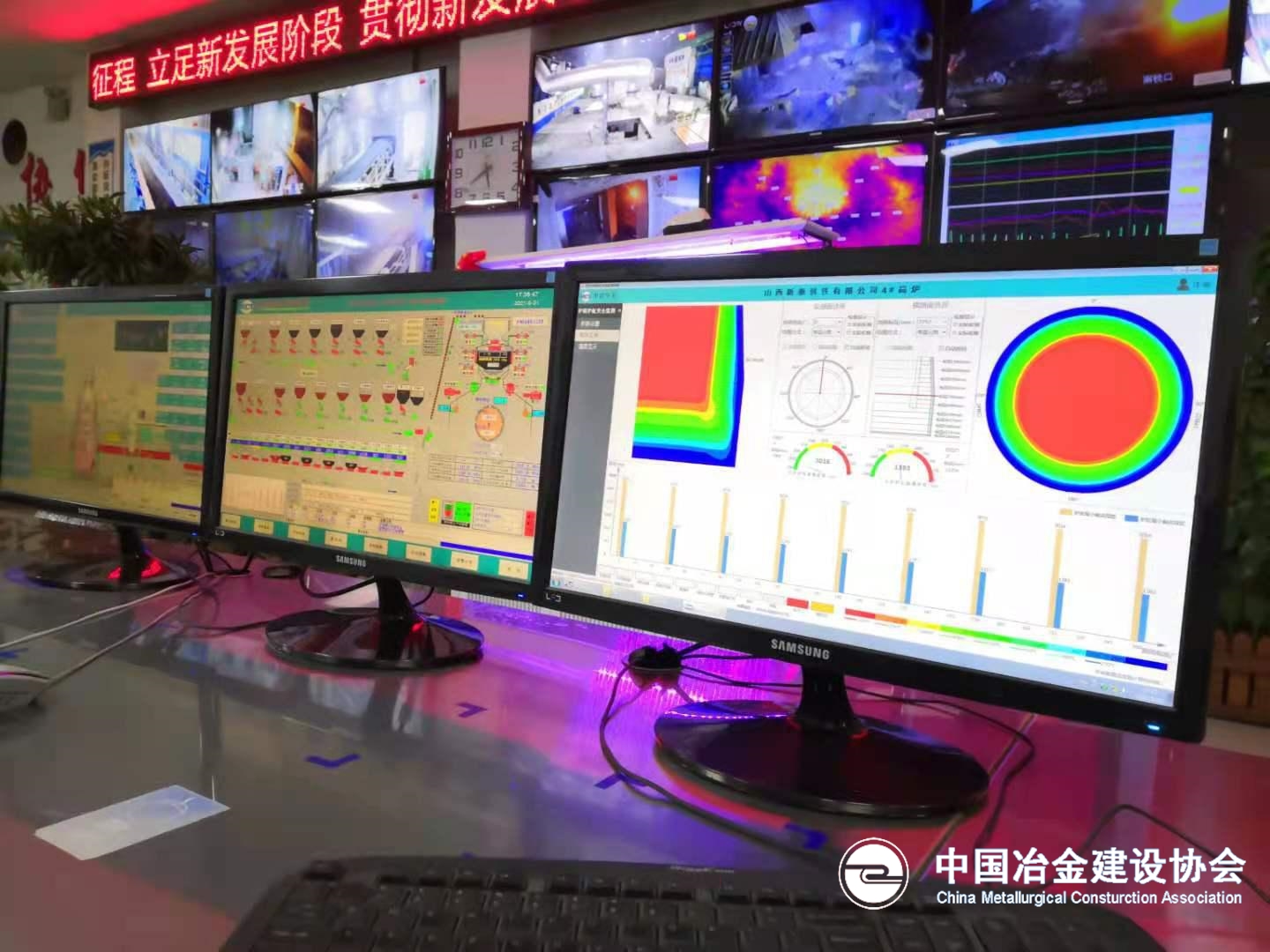
在高爐長壽、高爐智能化、高效熱風爐、節(jié)能環(huán)保等方面擁有獨特設計技術;掌握了當今高爐煉鐵所有先進技術,尤其在1000立方米-2500立方米級高爐中有較高的市場占有率和口碑……“我們始終站在國際水平高端和冶金行業(yè)發(fā)展前沿,憑借持續(xù)的自主研發(fā)創(chuàng)新能力、國際一流核心技術、冶金全產(chǎn)業(yè)鏈整合集成優(yōu)勢,引領中國冶金實現(xiàn)智能化、綠色化、低碳化、高效化發(fā)展,推動實現(xiàn)‘鋼鐵強國’目標。”7月7日,中冶華天鋼鐵院煉鐵事業(yè)部部長趙奇強自豪地說。
攻克“頑疾”保障安全穩(wěn)產(chǎn)
2021年11月,當“抗?jié)q防漏型高爐爐缸爐底綜合安全長壽技術”被中國冶金科工集團鑒定為“國內(nèi)領先”水平時,煉鐵事業(yè)部全體員工的艱苦付出終獲認可。
高爐爐底的密封性能直接影響高爐壽命,一旦發(fā)生問題不僅難以處理,還會造成重大安全隱患和經(jīng)濟損失。為攻克“頑疾”,中冶華天基于幾十年高爐整體設計和工程實踐經(jīng)驗積累,率先提出了基于爐底雙層封板結構,實現(xiàn)高爐爐底爐缸抗?jié)q防漏的新思路。經(jīng)過不斷研究、試驗,“抗?jié)q防漏型高爐爐缸爐底綜合安全長壽技術”脫穎而出獲得發(fā)明專利授權。該技術緩解了高爐上漲引起的爐底爐缸結構破壞和由此導致的爐底泄漏煤氣問題,一定程度上提高了高爐對焦炭、煤和各種礦石的適應程度,促進了高爐長壽、安全生產(chǎn)和環(huán)保。
目前,該技術已應用于河北安豐、福建三鋼、羅源閩光、永鋒臨港、河北華信、冀南文豐等十余座高爐。其中河北安豐鋼鐵2號高爐自投產(chǎn)至今,生產(chǎn)爐底爐缸溫度檢測正常,爐底爐缸狀態(tài)正常,爐底板無任何上翹現(xiàn)象,應用效果一如預期,實現(xiàn)了高爐穩(wěn)產(chǎn)長壽。
新技術實現(xiàn)放散煤氣和除塵灰零排放
高爐生產(chǎn)過程中放散的煤氣,為含有大量一氧化碳和灰塵的有毒、可燃物混合氣體,其放散時產(chǎn)生的噪音和粉塵不但對大氣環(huán)境直接造成污染,也浪費了煤氣能源。對于高爐爐頂料罐放散煤氣回收利用成為行業(yè)內(nèi)迫切解決的問題。
唯因其難,方顯真功。為攻克難關,中冶華天圍繞料罐與煤氣管網(wǎng)間壓差大、不穩(wěn)定及對管網(wǎng)沖擊大等技術難點,創(chuàng)新設計了新的均壓煤氣回收系統(tǒng)和凈化處理系統(tǒng)。通過應用檢驗,“高爐爐頂均壓煤氣凈化回收利用技術”可實現(xiàn)放散煤氣和除塵灰的零排放,放散煤氣回收利用率可達到80%-100%,高效解決了高爐爐頂均排壓煤氣及煤氣灰直接對空排放引起的大氣污染問題。
該技術現(xiàn)已授權發(fā)明專利1項、實用新型專利5項,應用于淄博鋼鐵、鞍山寶得鋼鐵、寶武馬鋼、河北華信、冀南文豐、福建三鋼、羅源閩光等多個大型工程。與傳統(tǒng)爐頂均壓煤氣直接放散工藝相比,年可回收煤氣千萬立方米、創(chuàng)經(jīng)濟效益達數(shù)百萬元。
自主研發(fā)助力綠色發(fā)展
傳統(tǒng)的高爐煤粉噴吹工藝系統(tǒng),存在瞬時輸送量波動大、生產(chǎn)成本高等缺點。中冶華天自主研發(fā)出了新型下出料濃相均勻自動高爐煤粉噴吹技術,通過獨特的工藝流程設計,實現(xiàn)高爐煤粉噴吹系統(tǒng)一鍵式自動均勻噴吹、濃相遠距離輸送,解決了自動化程度不高、輸送量波動大、輸送成本高等問題。
如今,這項被中冶集團鑒定為“國際先進”水平的技術,已成功應用于防城港鋼鐵、柳鋼、長鋼、河北華信、冀南鋼鐵等工程設計項目。寶武馬鋼二鐵總廠4座高爐年噴吹煤粉約130萬噸,可替代約104萬噸焦炭,節(jié)約煉鐵生產(chǎn)成本4億多元;采用濃相輸送可節(jié)省5000萬標方氮氣消耗,可節(jié)省煤粉噴吹成本約100萬元;采用自動噴吹后減員四分之三,年節(jié)約人工成本120萬元,且工作強度降低,減少了環(huán)境二次污染及煙氣排放,經(jīng)濟效益、環(huán)境效益顯著。
據(jù)了解,面對當前鋼鐵行業(yè)智能化發(fā)展趨勢,中冶華天正圍繞煉鐵高爐系統(tǒng)大力開發(fā)可視化、數(shù)字化和智能化相關技術,其中已突破部分技術并在生產(chǎn)一線落地應用,如“高爐爐底爐缸侵蝕智能監(jiān)測系統(tǒng)”已在鋼鐵企業(yè)實施應用;大力推進鋼鐵低碳技術的研發(fā)與應用,其中高爐噴吹焦爐煤氣的工藝設計、關鍵技術研發(fā)相關示范工程正努力推進中。(來源:中冶華天 黃蘋)