當前位置: |
以科技自立自強全力推動鋼鐵行業(yè)產業(yè)升級
——2021 年全國五一勞動獎狀獲得者中冶南方工程技術有限公司
    發(fā)布日期:2021-05-13
中冶南方打造的全球首個數智孿生料場——新余原料場
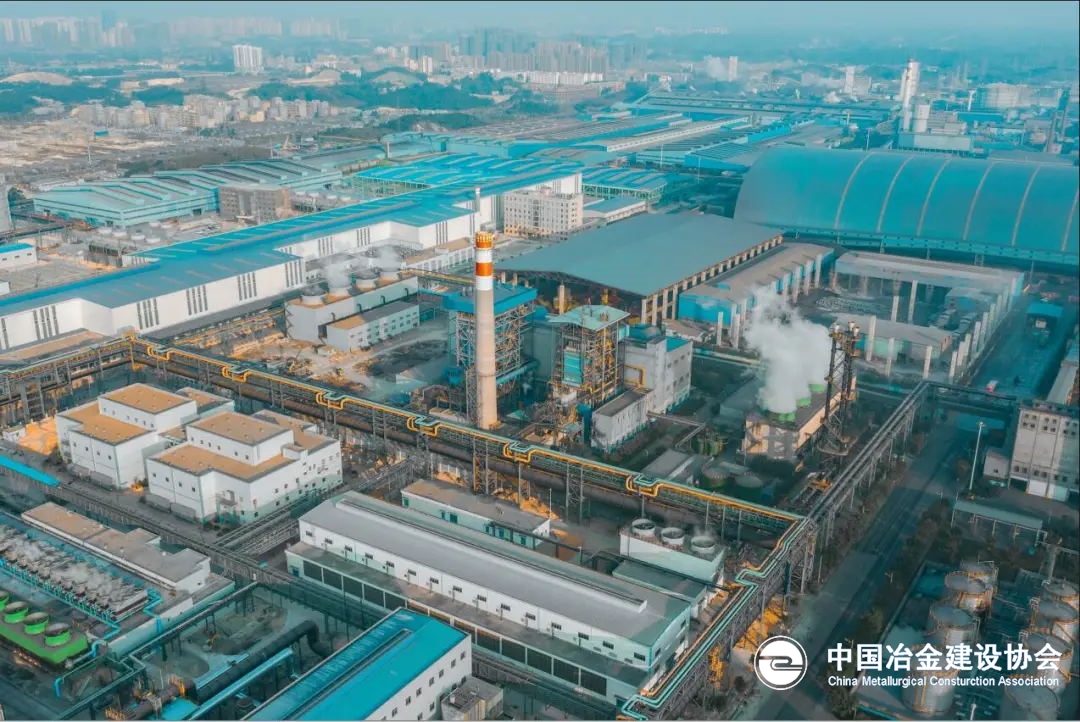
中冶南方實施的超高溫亞臨界100MW煤氣發(fā)電工程實景
新簽合同額與去年同期比增長28.4%,營業(yè)收入同期比增長31.77%,利潤總額同期比增長30.8%,這是中冶南方工程技術有限公司(下稱中冶南方)在第一季度交出的一份出色答卷。作為中國五礦、中國中冶連續(xù)多年保持高質量發(fā)展的標桿企業(yè),中冶南方獲得2021 年全國五一勞動獎狀。
全面踐行科技自立自強
去年5 月份,中冶南方以線上簽約的方式,與俄羅斯最大硅鋼生產企業(yè)新利佩茨克鋼鐵公司簽訂了新能源汽車用高端電工鋼連退機組購買合同,打破了歐洲公司長期在俄羅斯硅鋼市場的壟斷地位。該機組采用90%高氫退火工藝,產品覆蓋了新能源汽車用電工鋼的所有牌號,可處理厚度僅為0.1 毫米的電工鋼極薄帶,代表了目前電工鋼工藝裝備技術的全球領先水平。
2019 年,中冶南方在印度建成的世界最大不銹鋼連續(xù)生產機組——印度克羅美尼不銹鋼冷軋生產線,全線長700 米,工藝速度創(chuàng)世界第一,達200 米/分鐘,設計年產量70 萬噸,全部核心設備均由中冶南方自主研發(fā)設計成套供貨。
2020 年,中冶南方在連鑄高效化技術上再度實現重大突破,小方坯連鑄機拉速可達5.73 米/分鐘,達到國際先進水平,不僅節(jié)約了一次投資,提高了單流產能和勞動生產率,還降低了生產成本、能耗和廢棄物等排放。
今年1 月份,由中冶南方承建的世界最長鋼板輥底式熱處理爐——華菱漣鋼高強鋼熱處理線一期工程9 號線2 號回火爐順利出鋼。歷時200 天,中冶南方完成了2 條熱處理線、5 座熱處理爐的設計建設,以歷史最快速度打造出國內最大規(guī)模熱軋橫切板熱處理線,打破國外技術壟斷,實現高強鋼產品耐磨等級從300 到最高級別600 的穩(wěn)定生產和應用,引領商用車低碳化、輕量化發(fā)展新趨勢。
2 月份,中冶南方設計供貨的目前世界上連軋機架數最多、壓下率最大、單程軋制鋼帶最薄的冷連軋機組——青拓850 七機架不銹鋼全連續(xù)冷軋機組熱試投產,突破了傳統(tǒng)連軋的多個技術瓶頸。
強勢助力低碳綠色冶金
全力繪制碳減排技術路線圖,推進低碳、無碳冶煉,當前,中冶南方正與鋼企合作,開展高爐富氫燃料噴吹的工程探索,預計將于今年取得實質性成效。
在福建鼎盛、湖北金盛蘭,中冶南方相繼實施了5 座量子電爐建設,將于年內全面投產,單座量子電爐可實現碳減排70%~80%,節(jié)省綜合能耗45%~50%。
與此同時,中冶南方自主開發(fā)的具有全球領先水平的高參數小型化發(fā)電技術,已迭代升級至第五代超高溫亞臨界發(fā)電技術,可使全廠熱效率達41%,較傳統(tǒng)技術發(fā)電效率提升50%,已累計承接百余套,市場占有率達70%,在寶武集團寶山鋼鐵、武鋼有限、鄂城鋼鐵等基地,相繼承建4 臺超高溫亞臨界煤氣發(fā)電機組,可滿足每年30%左右的生產用電需求。目前,中冶南方正在推進第五代超臨界發(fā)電技術研發(fā),推動能源清潔高效利用技術邁向更高水平。
在不銹鋼領域,中冶南方自主開發(fā)的混酸再生技術于2017 年成功應用,全面打破國外公司的技術壟斷,在高效、長壽、安全等方面超越了國外同類型技術,占據國內外80%以上的高端市場。
深度融入智能化發(fā)展
在新余,由中冶南方打造的規(guī)模為64 萬平米、可滿足年產千萬噸鐵水生產的原燃料儲運需求的全球首個數智孿生料場,有近30臺(輛)堆取料機、卸料車等,24 小時連軸運轉,全流程一鍵操作,實現無人化智能協(xié)同、在線管控原料質量、降低原料庫存和儲運成本、減少資金占用。
在寧波鋼鐵,中冶南方打造的高爐數字孿生系統(tǒng),正在打開高爐生產的“黑匣子”。系統(tǒng)成功應用后,將可實施呈現爐頂布料效果,精確獲取氣流狀態(tài),及時診斷異常操作爐型,顯著提升煤氣利用率。
在寶武鄂鋼、武鋼,中冶南方投入使用的一鍵煉鋼系統(tǒng)、天車物流系統(tǒng)等,正在形成智能化煉鋼全廠整體解決方案,測溫取樣機器人、智能拆捆帶機器人、自動扒渣、無人化出坯等一大批智能化裝備也相繼在寶武、華菱漣鋼等多個項目中投用。
以科技自立自強為根本,中冶南方正在全力推動鋼鐵行業(yè)產業(yè)升級的進程中,踐行著大國央企的責任與擔當。?。ㄖ幸蹦戏健」└澹?/p>